We supply water to 2.3 million customers from our water treatment works through 9000 miles of pipes straight to customers' taps, but how does it move so seemingly effortlessly?
We’ve all learned the water cycle and its precipitation, collection, evaporation and condensation stages at some point. Water goes through a similar process from our source to your tap.
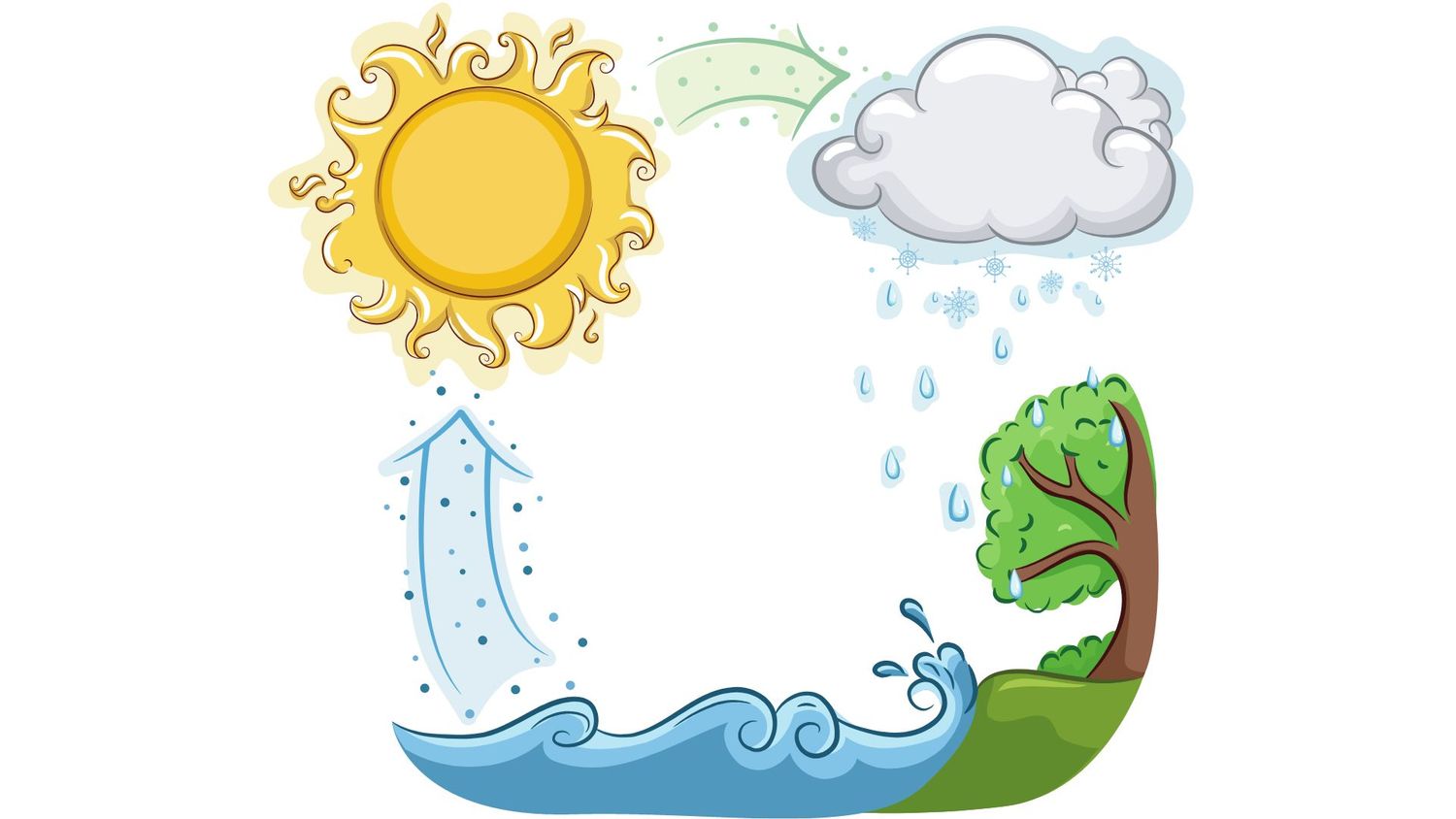
At South East Water, we have two main reservoirs in East Sussex, Arlington Reservoir and Ardingly Reservoir, as well as many smaller reservoirs and supplies we share with other water companies.
In the months when rainfall is higher and river flows are faster, water moves from the nearby rivers into our reservoirs, they’re also open, above ground, which means they also collect rainfall and run-off from the nearby ground. We also collect water from boreholes, aquifers and chalk streams.
The water then travels a short distance to our strategically placed water treatment works, where it undergoes rigorous treatment processes and tests to ensure the water is good enough to drink.
This is a very delicate process which relies on electricity for both the cleaning and supplying of water. Even though we have backup generators at many of our sites, after a short power cut, the equipment can take several hours to get back up and running.


Most of the water will then go to a storage tank or service reservoir, while a sample will be taken and sent to our Scientific Services laboratory for testing.
The laboratory(opens in a new tab) tests water from our reservoirs, customers' homes, and our water treatment works, as well as other water companies, hotels, swimming pools, and so much more.
The water goes through many more tests using state-of-the-art equipment as well as taste and smell tests. If the water fails the final taste and smell test, it has to go through the entire testing process again. Yes, we really do have a water sommelier!
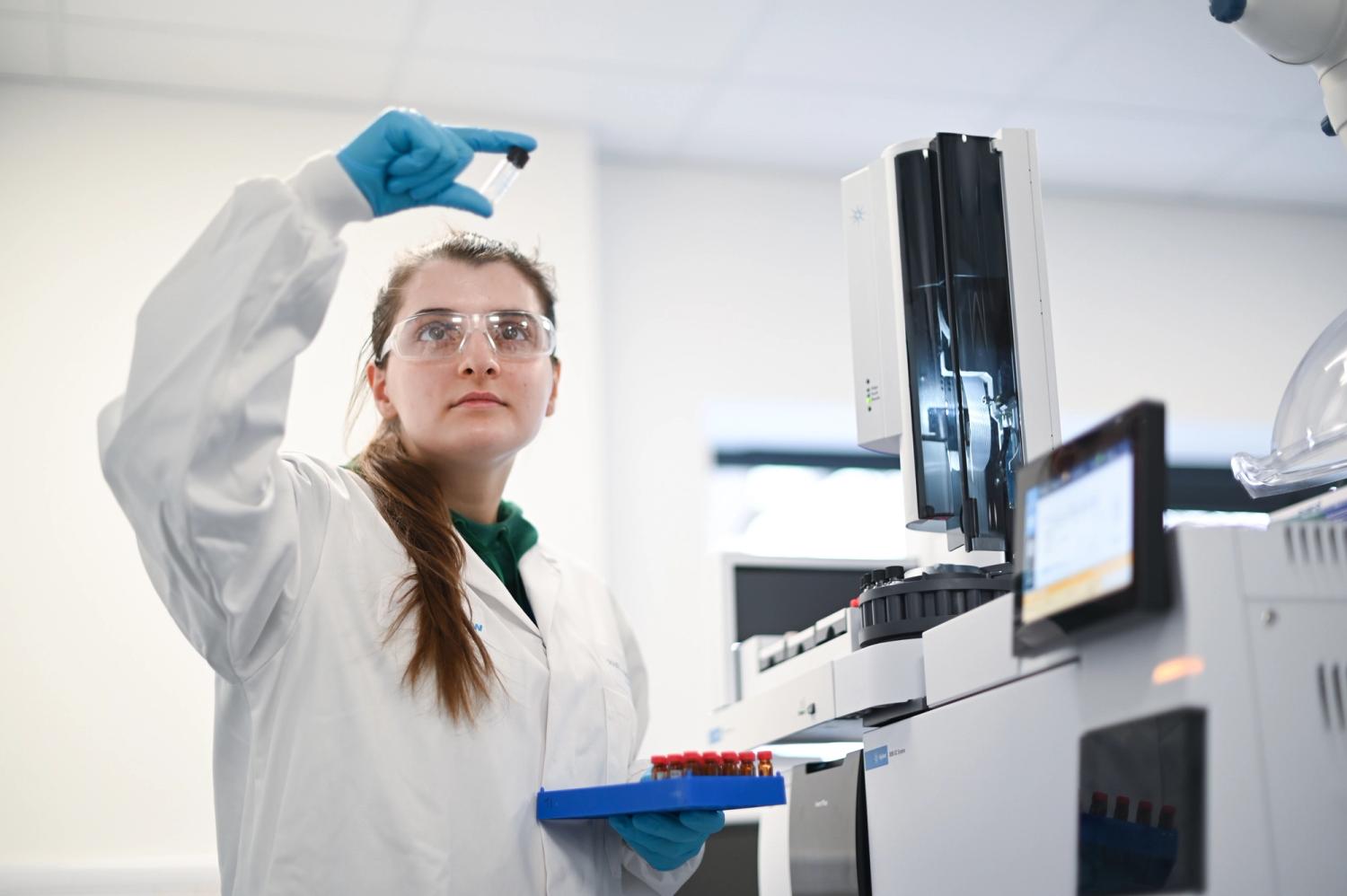
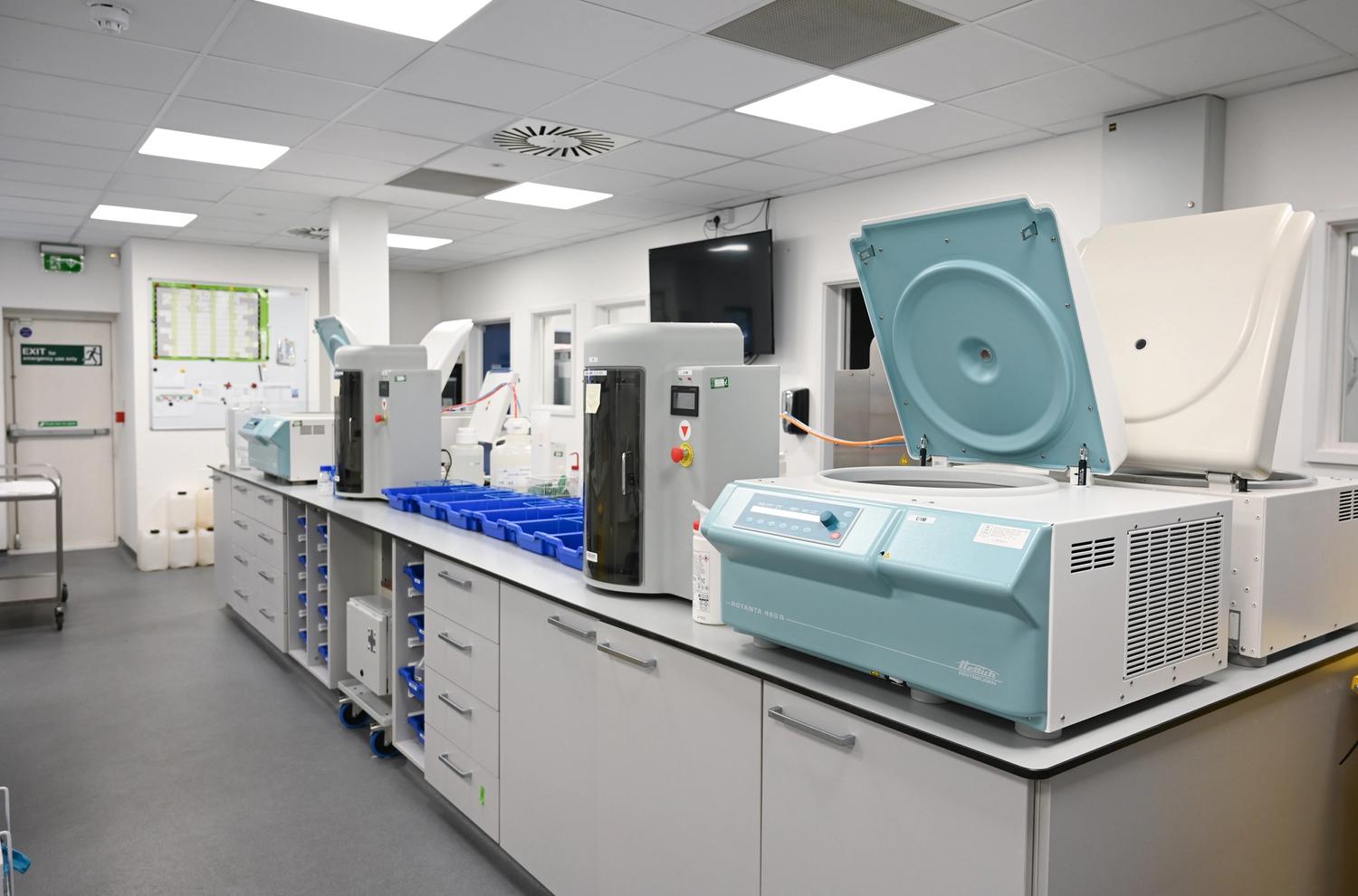
Once the water passes the regulations and tests, it's ready to travel from the storage tank or service reservoir through our network, being boosted through miles and miles of pipework to reach the farthest corners of our network. If you were to stretch out our pipework into one straight line, it would run from here to Australia.
Sometimes, our underground pipes burst for various reasons, causing the water to spill out before reaching customers' homes. Some people closer to the burst will experience pressure loss, while others will have no water.
Our control room monitors our entire network from their computers at our head office.
If they see a sudden change of pressure or surge of water leaving our reservoirs, they can alert our technical teams, and while we shut off the main to fix it, our controllers can re-route water from other areas to supply our customers at the push of a button.
Once the burst main has been fixed, we slowly refill the entire main with water. This is done slowly and carefully so the sudden pressure change doesn't cause another burst further along the pipe, and it can take hours to do. We call this recharging the main.
Finally, the water will continue travelling through the pipes to its final destination, our customer's taps.
The journey of water from its natural source to clean water in your taps is a long and complicated process. These steps are in place to bring the water up to a safe standard for you to drink.
Share this Article: